文 | 裴莉萌
编辑|白杨
巨型“铁钳”稳稳夹住火红透亮的钢锭,缓缓移送,朝着1.5万吨自由锻造水压机行进,交汇处,火花迸射,锻压声咣当作响……在中国一重的水压机锻造车间内,锻件周身散发着灼人的热浪,映红了周围一片。车间内机械林立,每一个炽热的锻件、每一台轰鸣的设备,都在诉说着中国一重执着于大国重器锻造的奋进故事。
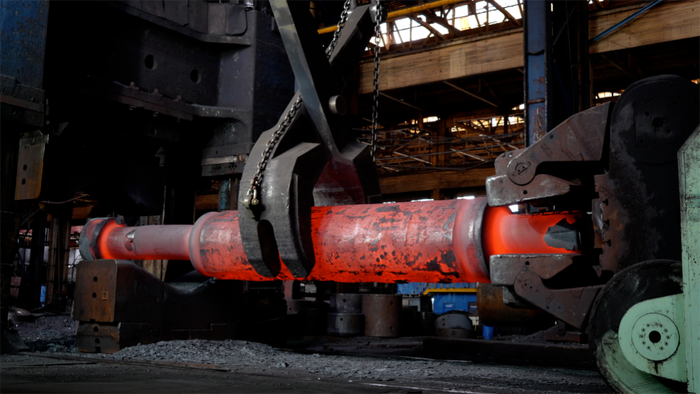
1958年,按照边建设、边准备、边生产的原则,中国一重炼出第一炉钢水、1960年成功研制我国第一台1150mm初轧机、1.25万吨自由锻造水压机……自诞生之日起,中国一重便肩负起“填补国家重大装备技术空白”的历史重任。在冶金、核电、石化、能源等关键领域,中国一重累计为国民经济建设提供机械产品600余万吨、开发研制新产品444项、填补国内工业产品技术空白584项,创造数百项“中国第一”,其打造的万吨水压机、核电压力容器等“国之重器”,成为中国制造业自主可控的稳固基石。
持续创新发力,夯实大国重器根基
回溯往昔,中国一重的发展壮大并非坦途。
2007年,在红沿河核电站1号百万千瓦变压器的研制中,核心一体化锻件遭日本技术封锁。核电常规岛整锻低压转子锻件是百万千瓦级核电设备中的关键部件,锻件尺寸、重量超大,对设备能力要求高,热加工工艺极为复杂,制造难度极大,“卡脖子”之痛如芒在背。
是退?是守?还是攻?
面对抉择,一重人毅然踏上自主创新的艰辛征程。
715吨级钢锭冶炼、400吨级毛坯锻造、20多米长工件精密加工……每一个环节都是工艺极限的挑战。为确保整锻低压转子材料性能万无一失,科研团队甚至不惜将价值不菲的锻件剖开,对材料进行金相分析,使用放大镜和显微镜观察研究材料的宏观和微观组织。
攻坚克难终有成,破冰斩棘铸成果。2012年8月,核电常规岛整锻低压转子锻件新产品通过了中国机械工业联合会专家组的鉴定。其研制成功表明我国已具备了提供合格的AP1000乃至CAP1400常规岛整锻低压转子的技术能力,对提升行业的锻造技术水平,打破国外对核电常规岛整锻低压转子锻件的垄断,降低造价,提高国际市场竞争力具有重大意义。
“没有百万千瓦整锻低压转子,以及‘一重’做锻件的大型产能提升,就不会有中国核电的大发展。”中国一重集团生产部部长助理孟祥东回忆道。
在核电装备领域,AP1000、华龙一号、国和一号(CAP1400)等三代核电反应堆压力容器的成功研制,实现了核岛主设备100%国产化。锥形筒体锻件是第三代核电蒸发器关键部件,实现了整体锻造,成为全球第二个掌握该技术的国家,锥形筒体制造技术解决了核电关键大锻件依赖进口的瓶颈问题。
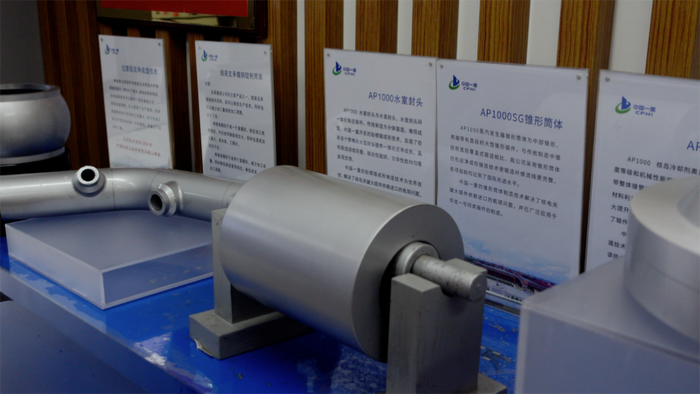
在石化装备领域,中国一重研制出全球最大的3000吨级浆态床锻焊加氢反应器,采用窄间隙焊接、整体热处理等技术,实现壁厚500毫米的超厚壁容器制造,应用于煤化工和炼油领域,替代进口设备降低成本40%。
在有色金属领域,欧美长期垄断钛、铝轧制设备,一重人另辟蹊径,从黑色金属轧制转向有色金属工艺研发,攻克钛合金锻造与热处理难题。
此外,中国一重在能源装备、冶金装备、材料科学与工艺、重型锻压设备制造等领域均有多项技术实现突破。
“我们倡导的理念就是在大的工件上,做绣花针的功夫。”中国一重集团科技部部长郑新毅坦言:“我们在攻克卡脖子问题的时候,基础研究的突破,才能够实现技术和产品的突破”。
中国一重与高校、科研院所紧密合作,依托哈尔滨工业大学塑性变形理论研究优化锻造工艺,与钢铁研究总院合作突破核电材料成份设计瓶颈,大连、天津等基地协同发力,形成“设计-材料-制造”闭环,不断夯实大国重器的技术根基。
加快数字转型,大力发展新质生产力
位于厂区中央的数据指挥中心,大屏上实时跳动着生产数据;在轧电数字化车间,34台数控机床组成了一条“隐形流水线”;在“一重专项”的数字化制造车间,无人值守的柔性生产线正进行着自动加工……
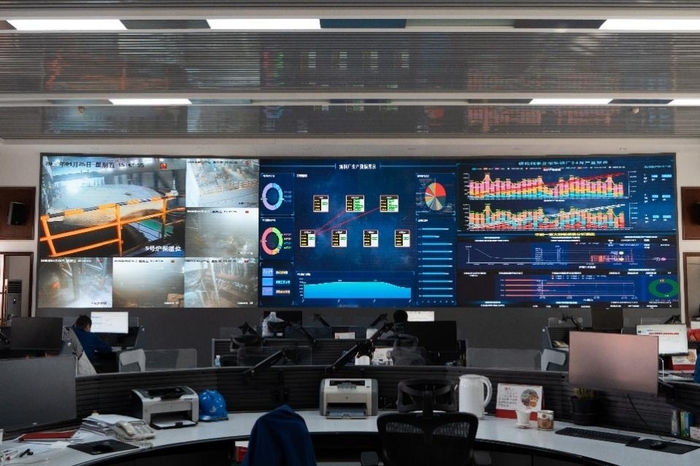
科技浪潮,奔涌向前。在全球产业变革与“双循环”新发展格局下,传统制造业正经历从“要素驱动”向“效率驱动”“创新驱动”的深度转型。作为大国重器的摇篮,中国一重以数字化转型为引擎,加速激活新质生产力,更以“领跑者”姿态重塑高端重型装备制造业竞争格局。
中国一重深刻认识到智能化转型的紧迫性。设备落后时,人力是弥补短板的主力,但智能化的本质是用数据替代经验,中国一重正将数字化转型作为核心战略,全力打通设计、生产、运维全链条智能化闭环。
“对于一重这样一个特种装备制造企业,面临的一个比较大的问题,是设备的先进程度不够,这就需要更多的靠人来弥补。所以我们在推进生产数字化和车间智能化的过程中,重点是对传统装备的改造升级,让它具备更多的自动化和智能化功能。”信息中心副总经理李学东说。
目前,中国一重共建设三个数字化车间。其中,大连专项智能制造中心的数字化车间,打通了专项产品的设计、工艺制造等整个业务流程,促进了专项产品的生产和保障能力的提升;轧电制造厂建设了基于5G技术的机床联网以及数据采集,积极推进了轻量的5G+UPS的下沉,实现设备的数据采集、电子看板、数据程序管理与传统传输和系统集成;在炼钢厂建立了大型铸锻件的洁净钢平台,打造了洁净钢生产的自动化、智能化制造执行系统,工艺过程的控制系统,产品的生产管理系统,实现了产品质量的稳定,大型高纯净,还有高效率低成本绿色环保的目标。
“中国一重的数字化转型情况,目前已经建立了两化融合管理体系、数据标准化体系信息安全体系。累计形成标准数据资源库数据量达540GB。”李学东表示。
中国一重将遵循数字化转型的战略部署,按照“十四五”数字化转型规划,统筹建设、分步实施、全面推进,解决好数字化转型的痛点和难点问题,续写“数字一重”建设新篇章。
打造产业链条,重构行业生态规则
国际竞争中,技术自主化是企业生存之道,更是重塑产业话语权的核心引擎。
曾被日本企业垄断的百万千瓦级核电转子,单根进口价高达8000万元至1亿元,国产化后价格节省75%;国际市场标价20万美元/吨的高端石化容器,如今“一重制造”仅需7万元/吨……中国一重以“打破垄断、重构规则”的担当,通过技术自主可控,维护行业价格体系公平。
“当核心技术握在自己手里,我们就从‘价格接受者’变成了‘规则制定者’。”孟祥东感慨道。
技术突破的价值,远不止于单一产品的国产化。中国一重将自身技术优势转化为行业赋能的“助推器”,通过构建“核心自研+外部协同”的产业生态,带动上下游产业链集体跃升。
中国一重联合30余家齐齐哈尔本地配套企业成立产业联盟,建立技术共享平台,从锻造模具的热处理工艺到智能仓储的物联网解决方案,累计输出200余项专有技术,帮助中小企业突破“精密加工精度不足”“数字化管理空白”等瓶颈,形成“龙头引领、集群发展”的制造网络。
刘伯鸣劳模工匠创新工作室作为基层创新“神经末梢”,更是成为技术外溢的核心枢纽。团队研发的核电主管道全位置自动焊技术、超临界转子表面强化工艺等12项“卡脖子”成果,通过技术培训、标准共建等方式辐射全行业,累计培养高技能人才800余人,推动整个锻铸产业从“跟跑模仿”走向“并跑超越”。
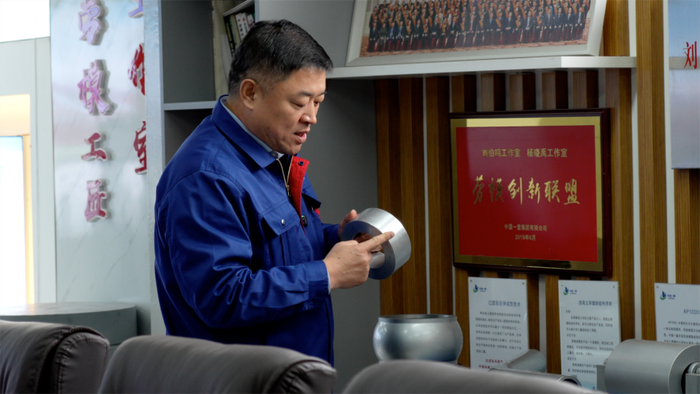
“最早时候可能是用270多吨干一件,现在250多吨就可以一次性干成两件,大幅提升了生产效率,降低了生产成本。”刘伯鸣轻轻拿起一个部件模型说:“利用一体化锻造成型技术,经过核算,为一家企业直接节约1.23个亿。”
此外,中国一重积极践行社会责任,在央地融合方面,投资光伏电站、核桃园、水厂,助力乡村振兴;在海外项目中,印尼青山产业园镍铁厂雇佣80%本地员工,让“中国方案”与属地发展深度绑定。
这种“链式反哺”带来的蝴蝶效应正在不断延伸并形成良性循环。中国一重的“锻锤”不仅锻造出大国重器的筋骨,更敲打出整个产业集群的竞争力,这正是“国之重器”对行业生态最深厚的反哺。
曾经,新中国工业化版图中的关键坐标,如今,“重”字的分量重新定义。中国一重正以技术创新为笔,数字化转型为墨,产业协同为纸,书写着大国重器的传奇篇章。
评论