记者 |
OPPO Reno在正式发布之前便因10倍混合光学变焦而受到关注。在手机拍照界面,用户可以轻易拖动变焦条,体验手机摄影的进步。但在这简单的动作背后,则是OPPO历经数年的投入。
近日,界面新闻记者前往位于东莞的OPPO工业园,近距离接触了整个生产过程,了解了OPPO Reno 10倍光学混合变焦版是如何制造出来的。
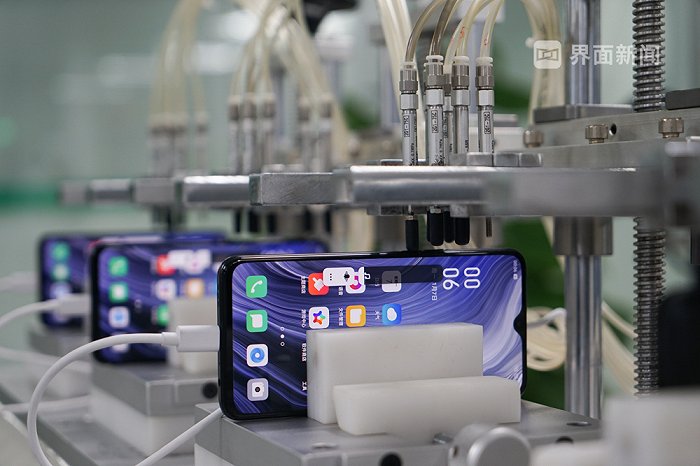
潜望式模组的共存难题
OPPO Reno的创新点在于,首次通过潜望式模组实现了10倍混合光学变焦,整个过程都在摄像头不突起的机身内完成。除了主摄有OIS防抖之外,潜望式模组的长焦摄像头同样配备了OIS滚珠光学防抖。搭配48MP的主摄与13MP的广角摄像头,三摄模组可覆盖等效16mm——160mm的焦段,并让画面像素保持在800万像素之上。
在普通消费者看来,或许Reno仅仅是做到了手机后盖不突起,却无从了解究竟OPPO是如何做到这一工程的。因为事实上,对于搭载了升降式模组和潜望式模组的Reno来说,想要把众多零部件全都在内部安排妥当,并保证机身后盖平整,在生产环节就会遇到不小的困难。
首先是厚度和空间利用。从设计的角度来看,升降式模组和潜望式模组占据了内部较多空间。在参观的过程当中,界面新闻记者发现,仅横置的潜望式摄像头模组体积就与主摄与广角摄像头加起来的体积相当。OPPO结构工程师坦言,一开始在升降模组和三摄模组的堆叠上,遇到了很大的难题。因为三摄模组设计之初有7.1mm,且升降模组与三摄模组占据了内部30%的面积。
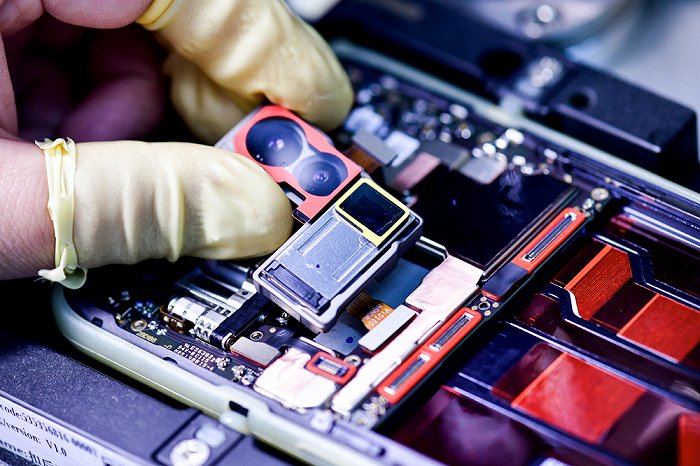
考虑到潜望式摄像头模组下的长焦Sensor是方形的,从圆形的镜片上透进来的光不会全部落在方形Sensor上,于是工程师决定干脆在潜望式镜头的边缘上切两刀——官方称之为“D-Cut工艺”,将模组的厚度整体降低到了6.76mm,还将长焦模组光圈做到了目前最大的f/3.0。此外,主摄与广角的镜头马达被合二为一做成了一个模组。镜头模组厚度解决了,中框也需要做相应的处理,OPPO将其中框设计出了凹槽,把三摄模组嵌入其中,最终达到背后镜头不突起的效果。
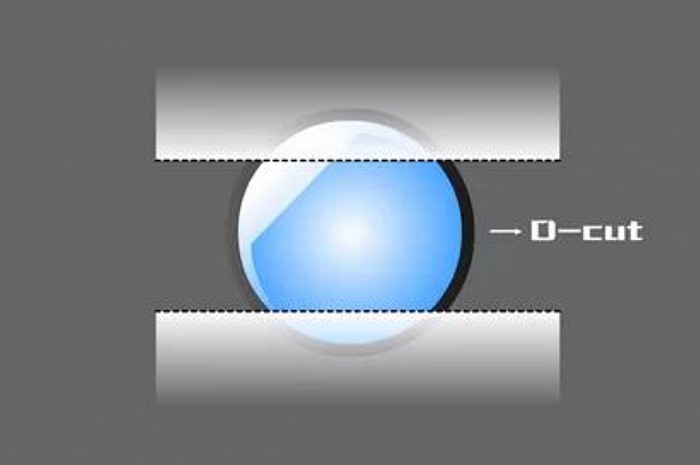
空间堆叠方面,Reno在升降结构上采用了U型传动装置+L型摄像头模组来合理利用空间,并把升降模组和三摄模组之间做到了4.75mm的安全距离。换句话说,这些零部件在市场上见不到,全部由OPPO专门定制。
其次是必须把潜望式模组与后背玻璃的开孔对齐,控制在误差范围内。由于玻璃背板包裹了整个摄像头模组,玻璃背板本身还分为表面玻璃层、遮光环、UV层CD纹理以及摄像头膜片镭切开孔。加上摄像头模组本身,总共有五个目标孔位需要对位,而每一个孔位都必须控制在0.15mm之内,否则就会影响摄像头最终的成像。这样的工序对于Reno来说是两倍或者三倍,因为Reno标准版后置摄像头是两个,10倍变焦版则是三个——最后一个孔是矩形。
因此Reno的不突起后盖带来了新的问题——摄像头上的玻璃必须为光面。而Reno的部分配色后盖大面积为磨砂雾面,这要求OPPO在一块玻璃上做出两种工艺效果。
据OPPO工艺工程师介绍说,一开始光面与雾面之间的交界线上,AG工艺有0.02mm的段差。虽然数值看起来很小,但在样品打印出来之后,手指仍能感觉到有轻微断层感。于是他们决定优化抛光工艺,把单面化抛改为双面的,这才将段差做到了0.01mm,最大程度降低了过渡层对手感的影响。
从“后盖不突起”的设计可以看到,在整体结构中,工程师们不仅需要考虑摄像头本身的放置,还需要协调内部各个零件之间的关系,多一点少一点都无法让手机达到标准,但是OPPO却做到了。
严谨苛刻的QE测试
OPPO Reno的不突起后盖,另一个方向可以理解为,普通镜头玻璃与后盖玻璃合二为一。而众所周知,镜头玻璃与普通玻璃并不相同,后者将带来眩光、透光率等方面的问题。OPPO影像工程师对此表示,经过专项测试,后盖玻璃符合光学成像要求,不会影响摄像头的进光。
不仅如此,OPPO的QE实验室还得对Reno进行随机抽样检测,样机被“蹂躏”一番后才能达标。
在QE实验室中专门有“防磨测试”,Reno需要经历5小时的石头摩擦测试和500次的桌面摩擦测试。
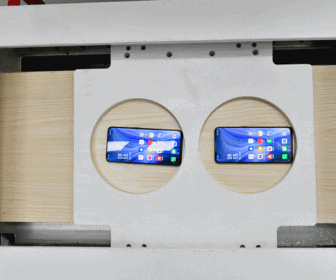
在参观过程中,我们还见到了多角度跌落测试、防尘测试、淋雨测试和压力测试等等暴力测验。即使类似于手机与牛仔裤摩擦这种场景,也被作为一个检测的环节,可见OPPO在正式把Reno递交给用户之前,已经考虑到了各类日常使用的场景。OPPO的这些检测标准已经超过了国标。
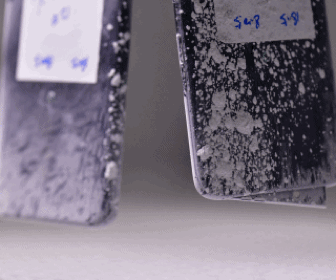
而在潜望式镜头模组的防抖方案上,OPPO同样采用了耐久的思维:Reno10倍变焦版采用了寿命更长的滚珠式光学防抖。
OPPO影像工程师向界面新闻记者透露,三四年前,OPPO就尝试过传统的悬丝光学防抖的测试,结果是可靠性不达标,大概经过几千次跌落后,悬丝会断掉。因此OPPO才用了滚珠式的光学防抖方案,其优点是陶瓷材质,有刚性的支持,相比较之下耐久度更好。
举了这么多暴力测试的例子,或许大家脑海已经有了工厂的画面:灰尘满天、工人戴着口罩......实际上却不是。与传统意义上的工厂不同,OPPO工业园区非常干净,车间对环境也有着严格要求。我们在进入车间之前,需要穿上防尘帽和防尘服,再经过一道除尘门。除了Reno“受虐”的QE实验室,OPPO此次开放了其他两个工作区域分别是SMT中心和总装车间。
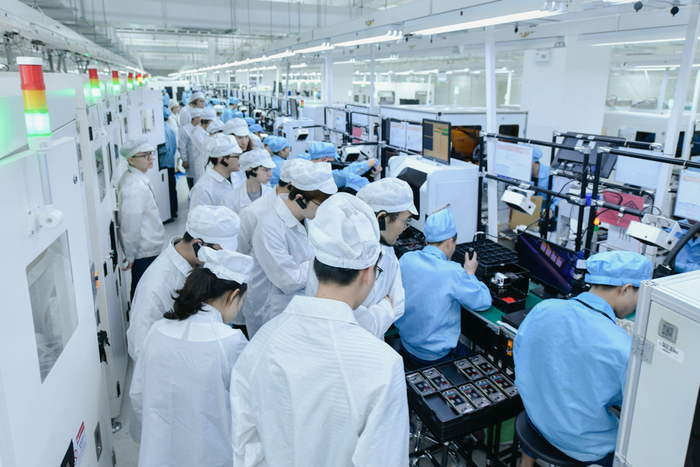
SMT(表面贴装技术)中心,主要负责主板的贴装,其大部分精细工作都由自动化机器人完成,每条产线只需要4名专业技术人员负责监控。在每道工序之后,都会有相应的检查机制,总共有18道品质检测工序来保证主板的品质。现场工作人员介绍说,在这种标准下的生产,SMT中心生产的主板良率能达到99.9%以上。
虽然绝大多数组装工作都交给了机器人,但由于Reno独有的侧旋升降结构、包含潜望式结构的三摄模组、线性马达等零部件的组装相对复杂,仅侧旋升降结构的组装就得18个步骤,因此生产过程中仍需要人工装配。在侧旋升降结构组装的生产线上,我们可以看见整条流水线的工作人员在与机器配合组装零件。在这个部分,产品同样会经过严格的检测步骤。手机最终组装完成后,Reno的侧旋升降式结构需要通过20次升降测试,OIS光学防抖还要经过抖动测试,才能被运出车间。
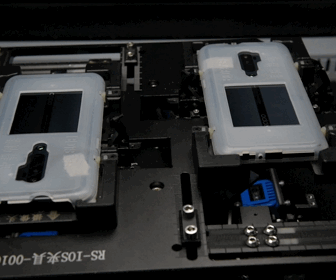
工厂参观的最后环节,OPPO特意将Reno的升降式结构部件交给我们自己安装。从零部件上可以看到,为了防止意外跌落损坏升降摄像头,在步进马达的连杆上还有一条弹簧用作跌落时的缓冲。算是打消了那些担心Reno升降摄像头牢固性用户的疑虑。
作为OPPO新产品线的第一部手机,Reno集合了OPPO的设计成果与生产实力。除了有10倍光学混合变焦技术,其实Reno还做到了前屏幕面板无可见开孔,把光线感应器、距离感应器都做到了屏幕下方;横向线性马达采用了专门定制的驱动芯片......Reno在技术上提升了使用体验,却把这些零件都藏了起来。在这些不起眼的思考背后,是OPPO多年来在制造上的积累和对每个环节的重视——或许很少用户知道,从一颗颗芯片电容到最终组装成型,并经过塑封包装出厂,一台手机会经历150多个测试步骤。
评论